Technical Description SCIP V
The main areas of SCIP V are covered in four tasks.
Task 1 is focused on fuel at back-end conditions, and aims at studying fuel and cladding performance issues related to interim storage. Fuel creep, hydride precipitation and reorientation, cladding annealing in long-term dry storage and treatment of failed fuel are the investigated areas.
In Task 2, issues related to loss-of-coolant accidents (LOCA) are studied. The aim is to study fuel and cladding behavior in LOCA scenarios, with focus on both standard and non-standard fuel, transient fission gas release, axial gas communication and microstructure and microchemistry related to fuel fragmentation.
Task 1 and Task 2 represent a continuation and extension of work performed in SCIP IV on back-end and LOCA issues.
Task 3, accident tolerant fuel (ATF), is a new area for SCIP and was requested by several members. The main focus is ATF cladding response to mechanical and LOCA type testing of ballooning and burst.
In Task 4, modeling support to the experiment planning and to the data analysis is given by the participants and will stimulate the understanding of important mechanisms related to fuel performance and dry storage.
Task 1: Back-end
Subtask 1.1 – Fuel creep
Whereas many creep and hydride reorientation tests of unirradiated cladding have been performed, hardly any data are available on the thermal creep properties of irradiated fuel rods with fuel pellets inside. In SCIP IV, a new test device was developed to perform creep tests with pellets inside, and a first test series was performed. In high burnup fuel rods, fuel-cladding bonding could restrict cladding creep out. In addition to the effects on creep behavior, bonding might also affect hydride reorientation behavior in the cladding, leading to local stress concentrations favoring local hydride reorientation and creating potential spots of crack initiation and propagation under long-term dry storage. Possible effects due to fuel-cladding bonding in high burnup fuel rods will be investigated. Creep properties of rod segments with fuel inside will be compared to defueled cladding properties. Test materials and test conditions are chosen to expand and complement the results from SCIP IV.
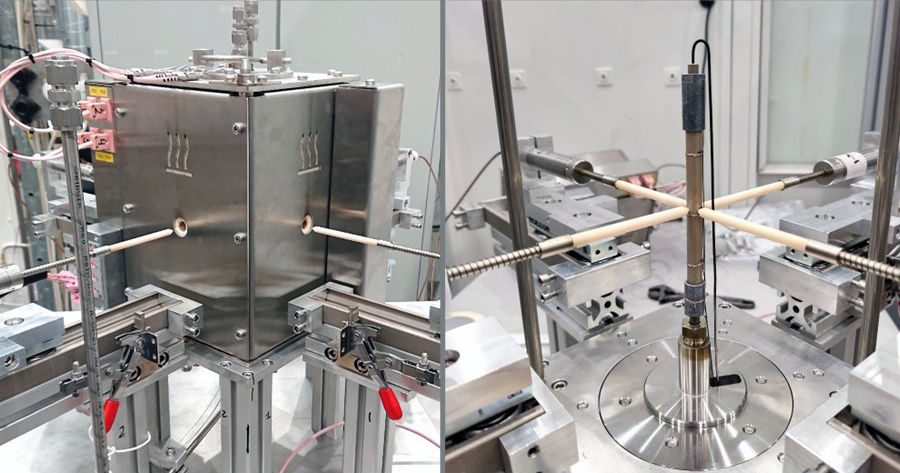
Subtask 1.2 – Hydride precipitation
During back-end handling and dry storage, fuel cladding temperatures will be high enough to dissolve hydrides back into solid solution. When temperature drops later on, hydrogen will be precipitated again. If the cladding is under high enough hoop stress, the precipitated hydrides will be oriented in radial direction, which impacts ductile-to-brittle transition behavior of the cladding material of concern. Current models on hydride precipitation in Zirconium alloys are normally based on the classical understanding that there are separate terminal solid solubility lines for precipitation (TSSP) and dissolution (TSSD). Recent experimental data obtained with different temperature-time profiles and novel methods raise questions about the classical description. Findings over the last decade show that pre-existing hydrides and cooling rates affect the required undercooling (supersaturation) for hydride nucleation. The objective of this subtask is to study the effect of pre-existing hydrides, irradiation and cooling rates, on the solid solubility lines for hydride dissolution and precipitation. The method to be applied is in-situ differential-scanning-calorimetry using the simultaneous thermal analysis (STA) equipment, a test technique recently installed in the hot cell laboratory at Studsvik.
Subtask 1.3 – Hydride reorientation
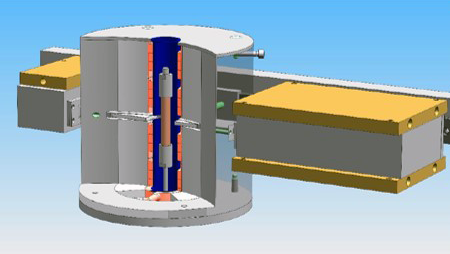
One main issue with respect to the cladding integrity during interim storage is formation of radial hydrides during cooling under internal pressure. Parametric studies for many years have generated significant amounts of data on hydride reorientation in most of the traditional LWR cladding types. There are still some areas, where additional data are needed in order to fully understand the hydride reorientation mechanism and the effect of radial hydrides on the ductility. Such areas include reorientation under very slow cooling rates, hydride reorientation in irradiated cladding material with low hydrogen contents, knowledge on which parameters are affecting the ductile-to-brittle transition and the microstructure of reoriented hydrides. To study these areas, reorientation tests of pressurized irradiated cladding tubes with controlled pressure and cooling rates are proposed. Focus will be on the influence of the cooling rate. Test samples will be studied by microscopy and ring compression tests.
Subtask 1.4 – Cladding annealing in long-term dry storage
At the end of its service in the reactor and its cooling in the pool, the fuel cladding is under internal pressure from fill gas and released fission gases. The cladding material, as-irradiated, is characterized by high strength and low ductility, compared to unirradiated material. During transportation and/or at the beginning of dry storage, the internal pressure may increase due to a rise in temperature resulting from fuel decay heat. If the rise in temperature is substantial, then annealing of the material may occur, reducing the amount of irradiation hardening. For irradiated materials, recovery of irradiation hardening (or material ‘softening’) can occur, if creep takes place at high enough temperatures, where annealing of irradiation damage may occur. Such a situation has been observed to lead to relatively early imposition of creep acceleration (involving an increasing rate of creep). The objective of this subtask is to study the conditions that could lead to creep acceleration during dry storage and the ductility change that accompanies it, and to determine the creep rate as a function of the annealing parameter for a given temperature and stress. This is planned to be performed on irradiated cladding tubes in two steps. First, the sample is annealed at a relatively high temperature without internal pressure to a desired level of annealing. In a second step, the sample is then pressurized, and creep testing is performed at a typical temperature and stress in the same test equipment. The secondary creep rate can then be determined as a function of hoop stress, temperature, and annealing level.
Subtask 1.5 – Failed fuel
In most countries, no standard procedures have yet been established to take care of failed fuel for interim storage and final disposal. For safe long-term stabilization of failed fuel, the radiological confinement needs to be restored and the geometry and environment needs to be controlled and stable. There are different concepts available to encapsulate damaged and failed fuel rods, either by canning in-pool or by conditioning and encapsulation at a hot cell. In this context, drying of failed fuel is essential to avoid gas generation by radiolysis of residual water and moisture. The presence of oxygen and hydrogen gas could have undesirable consequences, such as oxidation of the fuel, hydriding of the cladding, corrosion and pressure build-up. Whereas standards have been established for drying of intact spent fuel in dry storage casks, for failed fuel these standard drying procedures may not be sufficient to guarantee the required moisture level for encapsulation. Therefore, test methods to measure moisture content need to be developed and validated to prove that criteria on moisture content can be met. Furthermore, available drying procedures need to be evaluated for failed fuel and possibly optimized. Within SCIP IV, sections of intact and damaged spent fuel were dried in a hot cell using a custom-made installation for vacuum drying. The tests were performed on five different rods, using both BWR and PWR segments with varying burnup levels. The tests were performed at room temperature as well as elevated temperatures. Within this subtask, further experimental data on the issue of safe encapsulation and storage of failed fuel rods will be generated, expanding results of SCIP IV. Furthermore, advanced characterization of failed fuel will be performed, to improve determination of residual water content, to identify secondary phases near failure positions and to characterize the microstructure of failed fuel.
Task 2: LOCA
Subtask 2.1 – Fuel fragmentation, relocation and dispersal of standard fuel
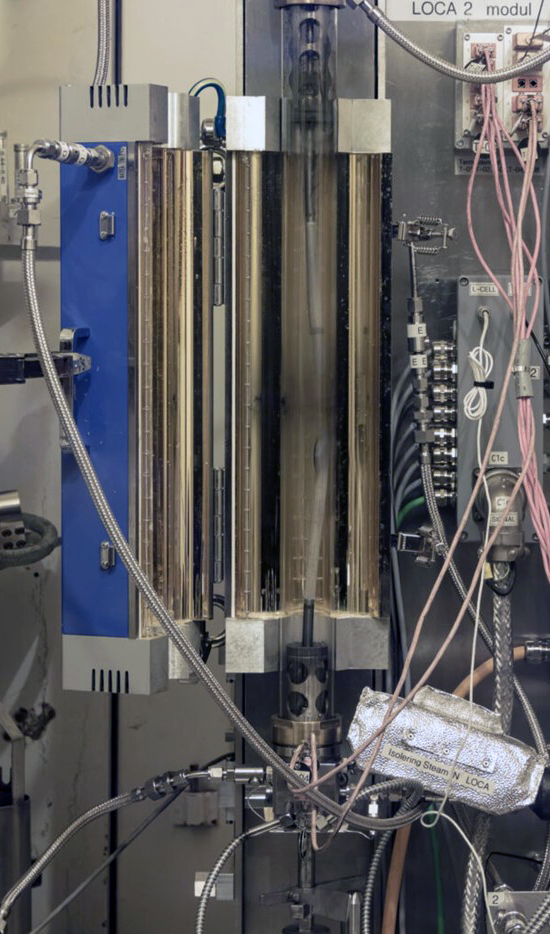
In previous SCIP phases, investigations on fuel fragmentation, relocation and dispersal (FFRD) were carried out to understand the performance of “standard fuel”. Numerous heating tests and many LOCA tests demonstrated that the degree of FFRD is not just dependent on burnup. Many factors impact FFRD during a LOCA. Parameters that are important include, amongst others, plenum size and gas pressure, temperature ramp rate, cladding strain and the size of the burst opening. Transient fission gas release might impact cladding strain during a LOCA transient as well. Some areas requiring further investigations were identified during SCIP IV, and also in a recent research information letter of the U.S.NRC and in an EPRI white paper. The amount of available gas in the plenum influences fragmentation. The temperature ramp may impact both the amount of fine fragmentation and the transient fission gas release. The plenum temperature may also influence the FFRD. In out-of-pile tests, the gas in the plenum is not heated. After burst, this gas flows through the hot fuel column and is warmed up. Finally, the number of tests with sample burnup below or close to the burnup threshold region is still limited. Work to be performed within this subtask aims at extending the database and improving the understanding of FFRD in standard fuel using integral LOCA tests and heating tests.
Subtask 2.2 – Fuel fragmentation, relocation, and dispersal of non-standard fuel
In previous SCIP programs, investigations on FFRD were mainly performed to study the performance of “standard fuel”, i.e., UO2 fuel with an as-fabricated grain size in the order of 10-15 μm. In SCIP IV, the focus was expanded to non-standard fuel types (e.g., doped fuel, Gd fuel, MOX fuel). More data is needed to understand the fragmentation behavior of these fuel types. It has been observed that increased burnup is not by itself the reason for fine fragmentation. Instead, microstructural changes in the fuel or other factors decide if the fuel is sensitive to fine fragmentation or not. Thus, additives and other changes done to standard UO2 might alter the evolution of the fuel during irradiation and therefore also the fragmentation behavior. Work to be performed within this subtask aims at extending the data base and improving the understanding of FFRD in fuel types that have not yet been investigated within SCIP III and IV, or elsewhere. The test methods used will be the same as those for standard fuel.
Subtask 2.3 – Transient fission gas release and axial gas communication
During a LOCA event, rapid and large changes of temperature may cause transient fission gas release from the fuel, by mechanisms such as fuel grain boundary fracture or diffusion and interconnection of fission gas bubbles. Understanding of the transient fission gas behavior is important to determine factors such as increase in rod inner pressure and margins to cladding burst and loss of rod integrity. Knowledge of the transient fission gas release also allows for a more accurate determination of the source term in an accident scenario. Transient fission gas release studies will be conducted within this subtask. In order to properly assess the effects of transient fission gas release on local pressure and ballooning and burst, it is important to know the axial gas communication inside the fuel rod. In SCIP IV, a test series was performed to measure axial gas communication against burnup and temperature. SCIP V aims to continue this work by adding more data that complement the existing tests. The results will support improving fuel performance code models of gas communication under transient conditions.
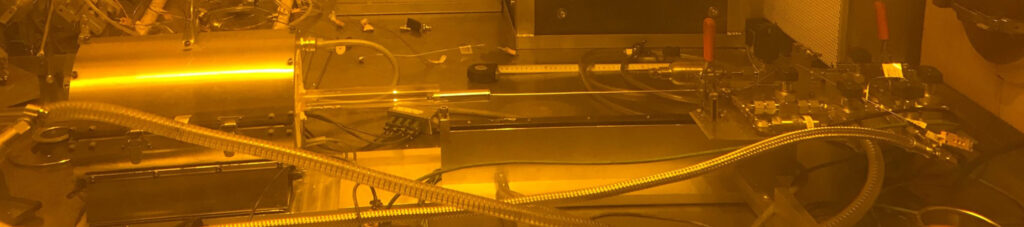
Subtask 2.4 – Microstructure related to fuel fragmentation
Results from previous SCIP phases have identified the potentially important effect of microstructural transformation leading to sub-grain formation also in the inner part of the fuel pellet. The sub-grain structure appears to impact fragmentation and was the focus of the advanced microscopy studies in SCIP IV. Most of the characterization in SCIP IV were carried out on samples that had not undergone transient testing. In SCIP V, similar studies will be carried out, also including more microscopy studies on transient-tested standard fuel samples. Grain boundary porosity has been shown to develop differently in additive fuels. Since the previous studies on fuel fragmentation indicated that sub-grain formation and fission gas content on grain boundaries are important drivers of fuel fragmentation, it is possible that fuel with additives will behave differently than standard fuel. For this reason, it is planned to complement macroscopic LOCA and heating tests on these fuel types with detailed microscopic studies. For this reason, the microstructure of non-standard fuel will be studied before and after LOCA transients and compared with the results from standard fuel. The studies will be carried out using scanning electron microscopy (SEM) together with electron backscatter diffraction (EBSD) and wavelength dispersive X-ray spectroscopy (WDS), to investigate local changes in microstructure and chemical composition. Laser ablation in combination with inductively coupled plasma mass spectrometry (ICP-MS) will be employed to determine the fission gas content before and after the tests.
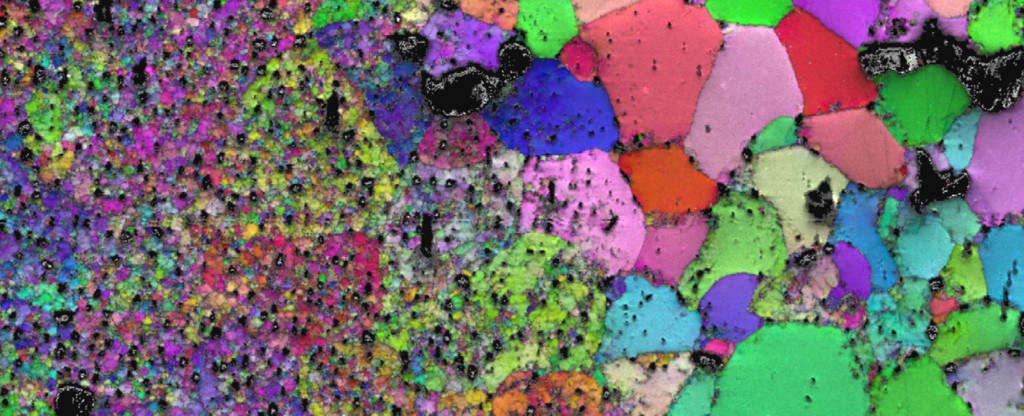
Task 3: Accident tolerant fuel
Subtask 3.1 – Mechanical properties of ATF cladding
So far, focus of testing novel coated cladding has been on the adhesion of the coating, on fretting behavior and on dissolution of the coating. Less data exists on the mechanical properties, especially on irradiated cladding. One issue that needs to be addressed is the effect of irradiation on the coating such as irradiation hardening, formation of cracks or local delamination, either as a direct effect of irradiation or indirectly as an effect of pellet cladding mechanical interaction (PCMI). The objective of this subtask is to test mechanical properties of coating and cladding in irradiated coated ATF cladding. The cladding integrity and coating condition will be studied by microscopy. This will be followed by different types of mechanical testing and post-test investigations. The mechanical tests will be done using existing test methods for irradiated cladding. The tested samples will be characterized by detailed microscopy. The focus will be on the impact of the coating on the mechanical properties of the cladding, and on how the coating and its cohesion is affected by the tests.
Subtask 3.2 – ATF ballooning and burst
Accident tolerant fuel concepts such as Cr-coated Zr-based alloy or FeCrAl cladding have been designed to have improved performance in normal operation and provide increased coping time during design basis accidents (DBA) and beyond-DBAs. It is likely that the balloon and burst behavior is affected as compared to standard cladding material. If the balloon is smaller, it would decrease the risk for flow blockage in the reactor. It would likely also decrease the fragmentation and relocation of fuel inside the fuel rod. Another potential benefit would be a small burst opening. Hence, this subtask involves investigating the balloon and burst properties of ATF cladding types, in comparison to standard Zr-based alloy cladding tubes. This will be done by performing integral LOCA tests to ballooning and burst.
Task 4: Modeling
This task aims at supporting SCIP V with pre- and post-test modelling calculations of tests and experiments using different codes and models. More specifically, the objectives are to provide input to the design of test matrices and to the selection of test parameters, to improve the evaluation and interpretation of experimental results, to extend the basis for the validation of existing models and to identify model improvements and the data needs for such improvements.